The pub shed project is under way and recently I laid the base for the cabin to stand on. But now it is time to start building The Cabin itself. So how hard is it to build a Home Bar cabin?
A shed is fairly easy to build, the floor goes in place, then the walls go up in solid panels. Finally the roof boards go on and then the felt. However a cabin is a little different, and in this article I will cover how I built the cabin to house my new home bar.
How Hard Is It To Build A Cabin?
It is pretty straight forward, and dare I say pretty easy to build a cabin. The best part is that because of the way a cabin goes together, it is possible to build it alone. Although it will be quicker with two people. First, lay your parameter bearers. Two, build your walls one log at a time adding windows and doors at the appropriate height. Three, board the roof, lay the rubber EDPM and fix facias. Finally, lay the floor and it is ready for use.
Sounds easy, but is it really that easy?
Step One: Setting Out The Parameter Bearers
The parameter bearers are basically what the cabin walls will sit on. Which means this is quite an important part of the cabin build.
They need to be the exact length and width of the footprint of the cabin walls. My cabin is 5m x 3m (16ft x 10ft). However because of the way a cabin goes together and the crossovers of the interlocking logs. The parameter is slightly less.
You would think that the bearers supplied would be pre cut to the right lengths, but they are not. Mine came in three metre lengths.
Therefore I put together the first row of wall logs and then made sure they were square by measuring the diagonals.
This gave me the exact length of the bearers and I could cut each side to size. I then put these under the first wall logs and fixed in place.
Once the diagonals are checked and adjusted it is time to get the walls up.
Step Two: Build The Cabin Walls
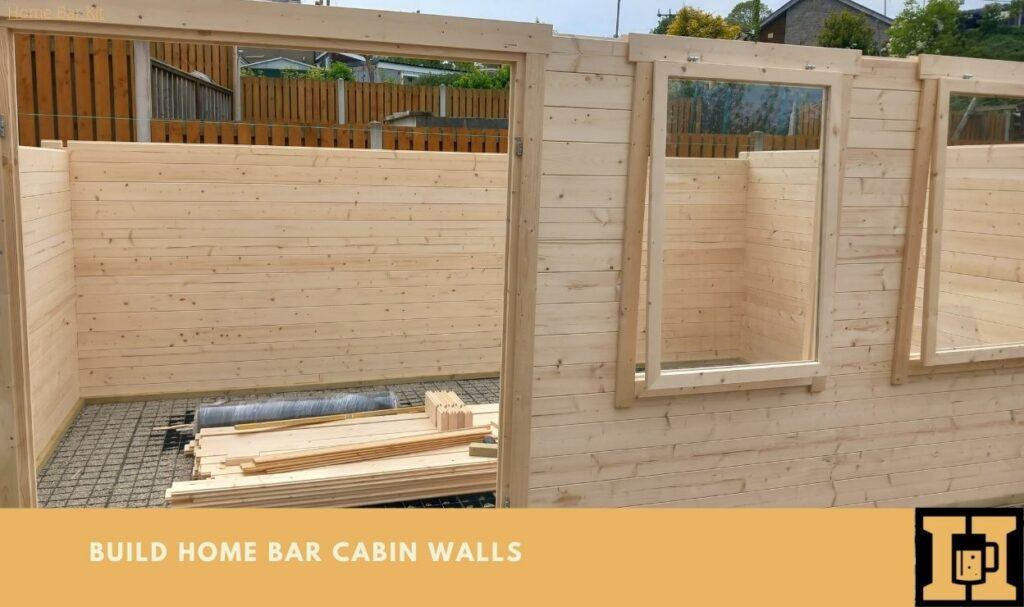
This is the fun part because the walls really go up quite quickly. The first layer, which I already laid and fixed to the parameter bearers have half logs on front and back, and full logs on the two side.
This offsets the logs and the walls are ready to go up. A full 5m log goes on the front and back coaxed into place by a rubber mallet.
Then a full 3m log goes on each side. Repeat this up to window height.
I have two windows and double doors to the front elevation. My windows are ready to go in at five and a half logs high.
At this point I did check again whether the cabin is still square. It did need a slight adjustment.
There are some short logs that go between the windows and the doors. I added four of these in each position to help support the windows once I lift them into place.
Which is what I do next, lift both windows into position and the door frame. At this point the front wall which is mainly the windows and door frame, is a little unstable.
Now it is a matter of just keep adding the other logs in sequence.
Once you get back to a full length log that goes on top of the windows and door frame, the front wall becomes more stable.
Another few rows of logs and the cabin is up to roof height. I then added the three roof beams, which really firm the whole cabin up.
The doors are easy to fit and just lift onto the hinges attached to the frame.
This is how it stayed for a week, as I didn’t have the time to put the roof on.
Step Three: Fitting The Cabin Roof
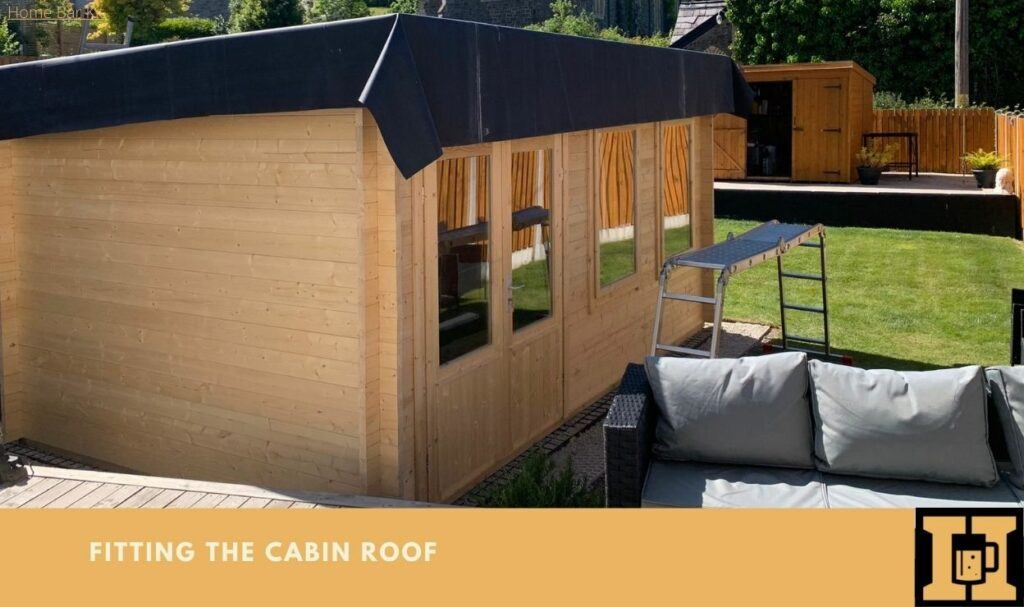
One week later and I am ready to fit the roof, but first make sure the cabin is straight and square. Again it needed a slight adjustment, which took a little while to get right.
My son Joe was coming for the weekend and after a six hour drive, within minutes of arriving was on the roof helping me fit the tongue and groove boards.
This speeded this up considerably. Each board, and there are a lot, need ten nails. So unless you have a nail gun, which I don’t, it takes a bit of time.
Then it is time for the EDPM rubber roof to go on top. Joe and I laid this over the roof and left it for half and hour or so to settle.
Then we roll one half back, lay the glue and then gradually roll the rubber back out again, making sure we get it nice and flat and bubble free. This is one part of the build that is a lot easier with two people.
Roof on and Joe gone, again the cabin sits tight for another week.
Step Four: Fitting The Cabin Floor
Unlike in a shed where the floor goes down first and the walls go on top. A cabin has a floating floor, which means you fit it once the cabin is built.
The floor is pretty easy to fit and independent of the walls. This means you do not fix any of the floor to the walls.
Although I have 3m floor joists they all need trimming because as I mentioned earlier, the inside footprint is less than 3 metres.
Each floor beam is laid with 400mm gaps to the centres. I then fit the insulation, which after a lot of research ended up being superfoil.
I have to say that it is very easy to work with and doesn’t require a storage unit to house it while you are waiting to use it.
Each board is now cut to size and laid in the opposite direction of the floor beams.
Floor down and just skirting to fit once I have chosen the floor covering.
Final Thoughts
So the actual build of the cabin for my new home bar was pretty straightforward. The most important part is to get the parameter bearers and first row of logs in the right position and square.
However it is a good tip to check the squareness regularly as it can move while building the walls. It moves less the more logs you add, I guess because of the weight.
Having said that, I still needed to make a slight adjustment before I started on the roof.
The same goes for checking the levels too, After each couple of rows I checked to make sure each wall was level.
This was only out slightly on a couple of occasions and is the result of one log not quite fitting together with the one below. A little coaxing with the rubber mallet is an easy fix.
The roof is also straightforward and ended up going on quickly because of the help of Joe.
Same as the floor, again straightforward with no problems.
So the cabin is now ready to transform into a pub shed. The next job is to build the bar, which will be made out of pallets and scaffold boards (supplied by Joe and friends).
If you have any questions, as well as tips too, then do share them below.
What Is The Best Size For A Pub Shed?
Update: This is how my pub shed looks today
My Finished Pub Shed
Rob is a passionate home bar and pub shed enthusiast with a passion for craft beer. With hands-on experience in designing and building his own home bar, Rob shares his knowledge, tips, and inspiration to help fellow enthusiasts create their own perfect space. Alongside the world of home bars and pub sheds, Rob also explores the diverse and exciting realm of craft beer, providing honest reviews to help you discover your next favorite brew. Join Rob on a journey of flavor, design, and craftsmanship right here on Home Bar Kit.